Filtering and Auxiliary Systems
Filtering and auxiliary systems are the unsung heroes that ensure purity and efficiency in the background, allowing the equipment to perform at its best.
Marco Pasotto - Technical Department Manager
MINO
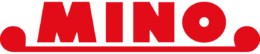
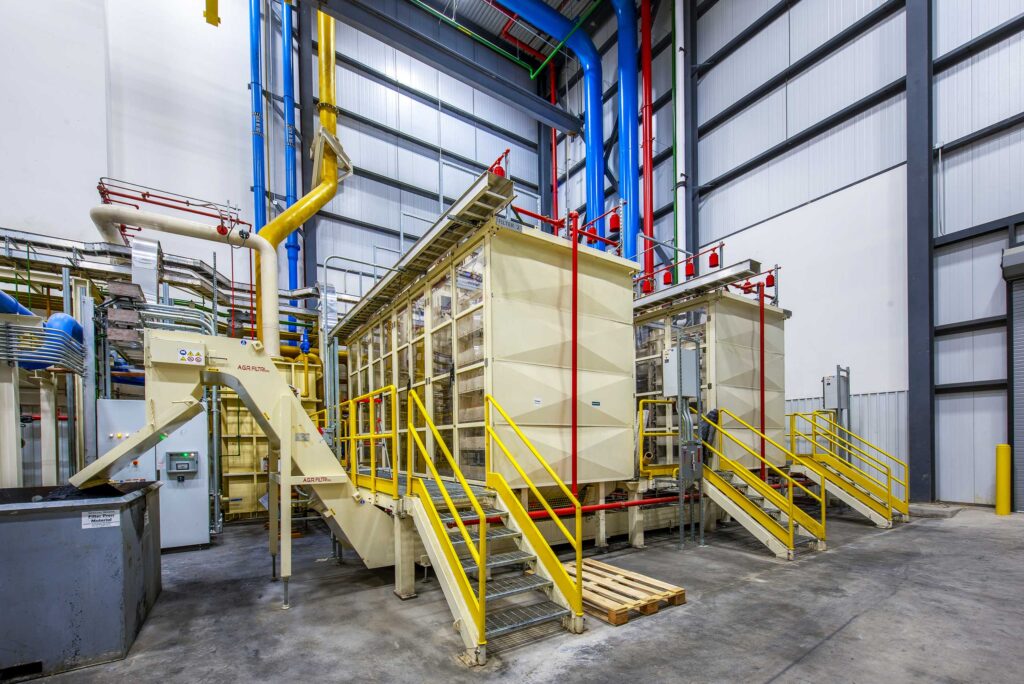
Filters
Rolling is a friction process generating heat, making essential the constant lubrication of the roll bite and the cooling of the work rolls.
It is easy to understand how important is for the Rolling Mills the filtration of the cooling media, prior to sending it back to the rolling stand to fulfil its function of lubrication and cooling, again and again.
Starting from the late 1960s, MINO have developed extensive know-how in design, manufacture and commissioning of coolant filters, that can be either Plate Filters or Bed Gravity Filters, depending on the metal to be rolled and to the type of rolling.
The Filters are not just guardians of the process but have direct effect on the rolling process and its results, both in terms of achievement of the final gauge and of the required strip surface quality.
Well-conceived and well-built filtration systems ensure quality, efficiency and productivity.
Filters remove impurities and contaminants from the Rolling Mill’s coolant, ensuring a pristine roll coolant to enable optimal rolling conditions.
Moreover, by effectively trapping particulates, filters prevent damage to work and back up rolls which are expensive and pivotal components of the mill equipment.
When filters are doing their job correctly, operators can expect reduced downtime and low maintenance costs.
They also give consistency to the quality of product and add value by eliminating contaminants that could compromise the surface quality of the rolled metal.
In the fast-paced world of Rolling Mills, Filters stand as an indispensable part of the process, discretely upholding production and quality.
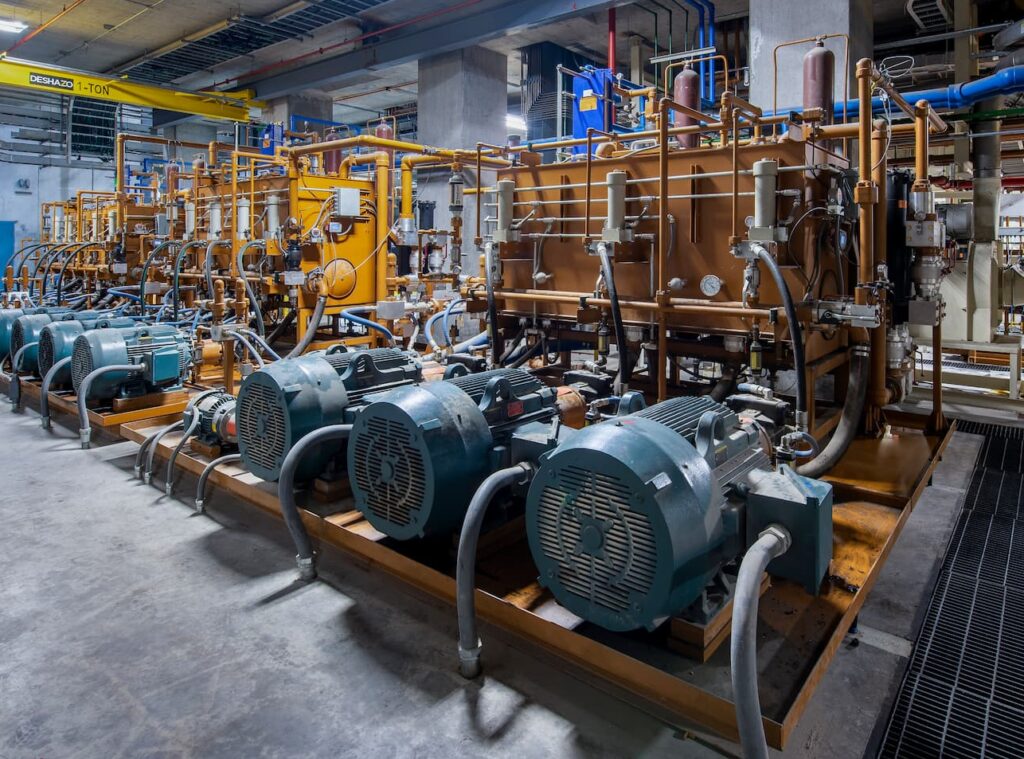
Auxiliaries
Auxiliaries fluid support systems for Rolling Mills are the unsung heroes of rolling industry, providing vital support to the equipment operation and reliability.
Our auxiliary systems encompass the functions of Cooling, Lubrication and Material Handling.
They ensure the Rolling process operates efficiently and reliably.
Cooling Systems prevent overheating, maintaining product quality and prolonging equipment life.
Lubrication systems reduce friction and wear, enhance precision and efficiency.
Material Handling and Storage Systems speed up the movement of raw materials, semi-finished and finished products, allowing a seamless carrying out of the Rolling process.
During the years, MINO have developed and realized different solutions for Material Handling and Storage, ranging from simple coil cars to more complex coil circulation systems (transfer pallet type) and to vertical high-bay systems having a storage capacity of up to 600 coils.
In the dynamic world of Rolling Mills, auxiliaries work silently in the background, enabling the Rolling Mill to work at its optimum, playing a crucial role in optimizing production, reducing downtime, and ensuring consistent quality in the production of metal coils.
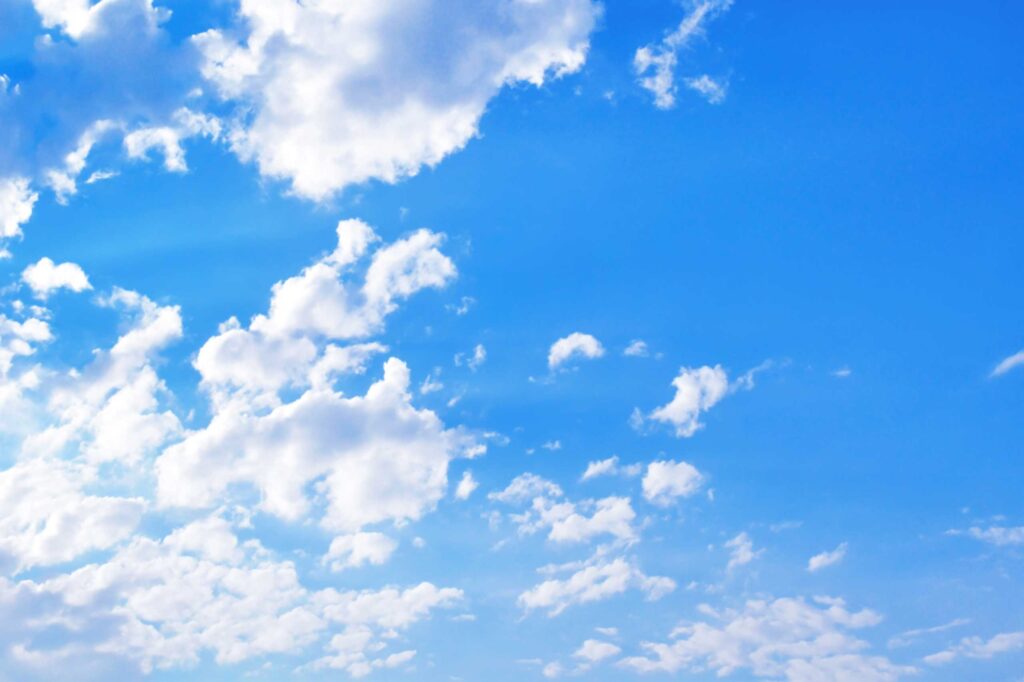
Fumes Scrubbing System
In the current drive to cleaner air, exhaust emissions are in focus as a source of pollution.
Rolling Mills produce exhaust fumes through the heat generated by the rolling process.
A fume Scrubbing System is now a necessary part of a modern Rolling plant.
With new environmental regulations demanding cleaner emissions, these systems meet environmental standards and additionally improve the working conditions of operators in the rolling area.
The process improves any exhausted vapours released into the atmosphere by removing harmful VOC’s (volatine organic compounds) which are regarded as pollutants.
These are generated during the Rolling process.
The washing and scrubbing tower ensure compliance with the latest environmental regulations.
Fume Scrubbing Systems also contribute to cost savings by capturing and recycling valuable fluids, otherwise discarded.
This recycling provides a qualified payback to the investment in such systems.
In conventional rolling mill plant many tonnes of roll coolant are lost in the exhaust systems to open air.
By installing a fume washing and recycling system, plant managers can rely on rapid payback of capital investment, coupled with ongoing savings in consumption of roll coolant.
Responsible plant managers now understand the benefit of not just protecting the environment, but also the health of those working in the Rolling plant.
In the ever-evolving landscape of Rolling, Fumes Scrubbing Systems play a pivotal role in advancing sustainability and safety.