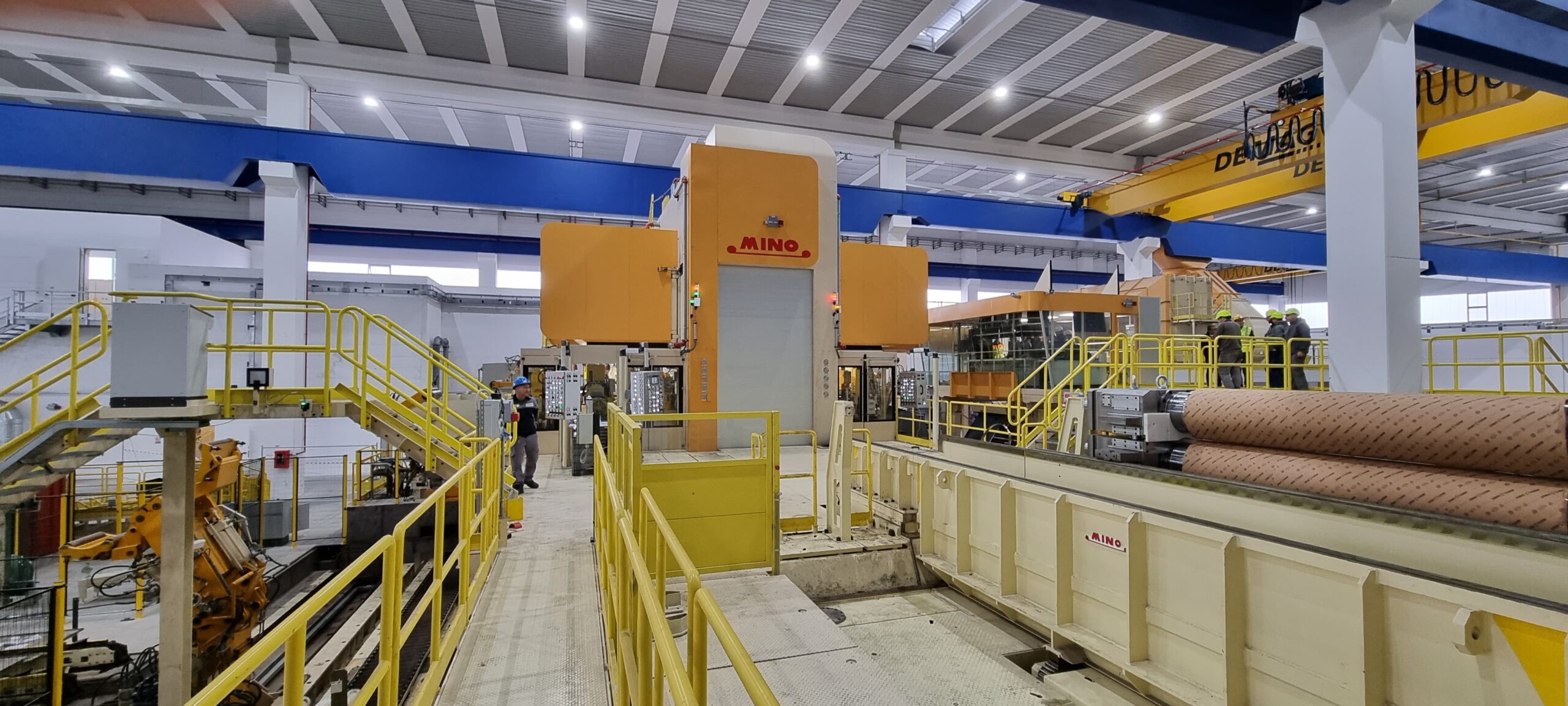
Italy’s biggest Cold Mill for aluminium is in full production!
The new state-of-the-art, extra-wide, MINO Six-high Cold Rolling Mill installed at Profilglass’ plant in Fano, on Italy’s Adriatic (east) coast, is in full production. Through this new investment, Profilglass is aiming at serving the most highly demanding industrial sectors (including car, construction and shipyard industry) with top quality aluminium